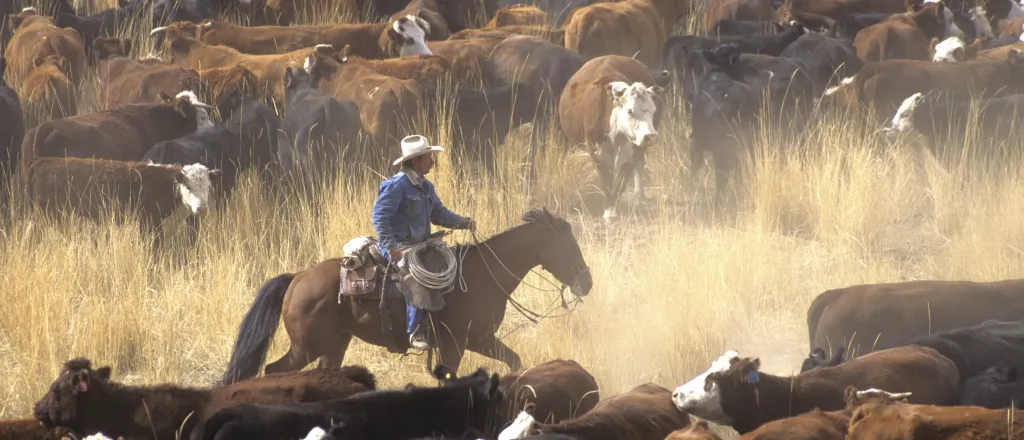
Transcript
[Music] Welcome to the Pasture to Profit podcast.
I'm Colorado State University Extension Specialist Scott Stennett, and today on Pasture to Profit we have our guest, Ms. Libby Bigler, who is the Coordinator of Colorado Beef Quality Assurance.
So welcome Libby, we're glad you're here with us today.
Can you kind of tell us a little bit about what you do with Colorado BQA?
Yeah, thanks Scott.
Thank you for having me.
I'm excited to chat with you today a little bit about some BQA topics, but as Scott said, I am the State Beef Quality Assurance Coordinator for Colorado, and so my job is to go across the state and talk with cattle producers about best management practices that really influence the quality and safety of the beef that they're producing so that our consumers can have confidence in the products that they're buying from us.
So day to day, you know, I'm traveling across the state, I might be going to a county cattleman's meeting, or I might be at a feedlot or a specific ranch, and I provide Beef Quality Assurance certification training.
So after about a two hour session, producers will take a quiz and they'll be certified in Beef Quality Assurance, and then folks can use that to market their calves or, you know, a packer may be requiring a BQA certification from their feedlot suppliers.
And so it's just an opportunity for producers to learn a little bit more about what they're doing every day and how that influences their product and maybe make some changes that can help enhance consumer confidence in beef.
Great Libby, and with that being said, it's about to be branding season here in our part of the world, eastern Colorado, and there's a lot of things we need to keep in mind to make sure that we're following some quality assurance guidelines when we're doing branding.
So what do you feel like are some of the highlights of things that we need to do for proper quality assurance when we're branding?
Yeah, branding time is a really good time to start thinking about Beef Quality Assurance.
I think sometimes people think about BQA as being something that needs to happen only at the feedlot, but really we can influence the quality of our meat product, of cattle, from the time they're born all the way through the feedlot.
So if you're branding, there's a lot of opportunities to think about animal welfare and meat quality.
And really, I think one of the most important things to think about is having a preparation meeting, right?
You know, a lot of times branding is when, you know, it's kind of a community event.
You always brand on Memorial Day weekend every year, and you always invite the neighbors, and you get as many people as possible there to try to help things go as smooth as they can.
I think the challenge is, though, if you don't have a meeting to prepare everybody and make sure that everyone knows what your expectations are, of how your cattle are handled, or how shots are given, or a number of different things, we're going to probably have some snags that make things go a little bit slower than we thought.
So, you know, making sure that we prepare everybody, we get everybody sat down and we know, you know, this is our expectations of this branding, here's how we do it, you're going to be roping, you're going to be actually applying the brand, you guys are giving the shots, making sure that we know what is expected of that.
And that could be anything from, you know, if you're the kids and the kids are always giving the shots, having somebody overseeing those kids in giving the shots and making sure they understand what a subcutaneous injection means, and they understand what the dosing is, and they, you know, they understand safety.
I think safety, human safety, is just as important as well.
So some of those things, making sure we prepare and we organize ahead of time, I think is really key.
And then, you know, getting into some of the specifics of BQA in that planning meeting is really important as well.
Yeah, everybody kind of knowing what their job is, I've, you know, I've been invited to help with, you know, our family brandings as well as neighbors and friends.
And yeah, some of them are just big social parties with a few people doing a whole lot of work and a lot of other people doing a lot of fun to ones that are, yeah, we're here to do this and get this job done.
And it's very, very quick, very efficient, but making sure that everybody has a job and everybody's doing their job properly and safely, not only for the animals, but for the people involved as well.
And speaking of the animals and some of the things that we do, you know, a lot of things we're not only doing, giving our shots, our vaccination stuff, but we have to do some things that can cause some stress to our calves.
We're going to brand, castrate, maybe even dehorn.
And we get a lot of talk coming from outside of our industry from folks in the general public concerned about pain management when we're doing these things.
So would you touch on, you know, some of the things we're looking at on pain management?
Yeah, so from a BQA perspective, the program is always looking at the most recent research to help guide, you know, what beef quality assurance guidelines look like.
And so in recent years, particularly as animals, I guess as consumers and general public have started caring more about, you know, where cattle come from and how they're cared for, all of those kind of components, we've started to look into the idea of providing different pain management for some of these painful procedures.
And so, like you said, Scott, you know, applying brands obviously is probably painful as well as castration and dehorning.
And so there is some research out there that shows there are some opportunities where we could potentially have some pain management for some of these procedures.
The big important thing here is, though, that we really want you to consult with your veterinarian.
Having a valid veterinary client patient relationship is key to BQA.
So a VCPR is very important.
And some of this pain mitigation medications that are on the market, specifically meloxicam is what I'm talking about, is off label.
And so you have to have a veterinarian, first of all, to consult you as to whether or not that's something that might work for what you're doing on branding, at branding time, but also to get you the product itself is really important.
So meloxicam has proven to help with pain mitigation for up to three days after the procedure.
It's little bitty tablets and they're based on weight.
And you can just put those tablets in those gel capsules and bolus them.
And so although it may not provide any pain mitigation in the moment.
So when you're actually doing the castration, it will provide help for up to several days afterwards.
And they see good results about calves getting back on feet and things like that quicker.
Now, when it comes to actually applying the brand, there's limited research on whether meloxicam is helpful.
But if you're already castrating and dehorning, it's probably not going to provide any negative consequence from the brand standpoint.
There is research that show like a lidocaine block on that brand area doesn't really help necessarily and actually might have a negative consequence on how that brand actually turns out how it heals.
And so I would say if you're going to talk about pain mitigation, you know, of course, talk to your vet, see what they think.
But meloxicam might be the one that works the best and your veterinarian will help you consider that if that's an option on branding day for you.
And even in a lot of the things that we put out through extension and you put out through BQA, we talk about these things are stressful and the bigger the calves are, the more stressful it appears to be on them.
So we want to remind folks to also try to do their branding as early as possible.
We would all love to have a nice 30 day calving period.
But if you're moved your calving times up and you're still having that Memorial Day branding, now they're 30 days older than they were.
And so it's going to be a little bit more stressful and stress causes losses in gain and efficiency for a couple of days when they go backwards because they've been stressed through the branding process and getting their vaccinations, everything.
So, again, we want to make sure that folks think about that and let's do these things to these animals as young as possible.
Yeah, absolutely.
That is a kind of a core principle of BQA.
You know, in the history of BQA, if you were to open your BQA manual and look up these procedures, branding, castrating, dehorning, the guidelines say do it as early as possible.
Your earliest handling opportunity would be the ideal time to do it.
But if you do have to wait, make sure that you're doing it appropriately.
So make sure you're trained and applying, you know, applying brands expertly.
You don't get them too hot.
You're not holding them on the hide too long.
Things like that because we want to reduce stress as much as possible.
And if you couple that with the fact that we are typically giving vaccines at the same time, you know, additional stress is going to reduce your immune response.
And we really need an immune response to make sure that our vaccines work.
So the least amount of stress that we can have during branding to make sure that the vaccines work is ideal.
So those are some things to kind of keep in mind to make sure everything works together well and we get the outcomes that we're looking for by getting our cattle together and branding and doing those early vaccines at that time.
Right.
And we keep throwing the term branding out because here in Colorado, we are a brand law state.
And there's some important things we have to remember about the location of those brands.
So not only is there some legal ramifications to where we brand, but what is it on the quality assurance side as far as proper branding location?
Yeah, so if you think about the mission or the goals of BQA, it's to really enhance meat quality, safety, and those kind of things.
And so sometimes people think, well, the hide isn't really meat quality, but if we can maintain the quality of those hides, we're going to get more money in the long run for the entire animal.
And so when we talk about branding, the idea that we want is to make sure that we're not putting a brand somewhere on that hide that will make it less useful when it becomes a piece of leather, whether that's a BMWC or a purse.
And so if we can put that brand kind of up high on the hip, that's going to be a really easy location to get rid of that piece of what we would call damaged leather at that point.
It's not damaged in our hearts because it's part of our identity as a ranch.
But once it gets to that next phase, we need to make sure that it's easily removed.
And so the BQA guidelines say try to brand them up high on the hip if we can.
We know that in some brand states, you do have a location that's tied to your actual brand.
And so you may have to do it on the rib or the shoulder.
But we absolutely do not want any brands on the face or jaw from a welfare perspective that becomes problematic.
If you do have to apply it in an area other than on the hip, just like I said before, make sure you do it expertly.
You do it quickly.
You're considering how hot your irons are getting and making sure that we're reducing the amount of stress on those animals when we actually apply the brand.
Another thing to think about would be if you can get your entire brand on a single iron so that you're only applying that hot iron one time rather than two or three times to make that character appropriately, that would be helpful as well.
Just help reduce stress in the long run.
Right.
And so again, that branding can cause some stress and we're worried about some immune response because we're going to give vaccinations.
But properly handling our vaccines is as big a deal as the stresses of branding and castration.
Let's talk a little bit about what do we need to think about when we're handling our vaccine products?
Absolutely.
There's so many moving parts here.
We think about everything that needs to go on during branding and trying to make sure that everything works well.
Vaccines are pretty fragile.
There's a couple of types that we use.
Everyone that's doing the vaccination during branding needs to understand what type of vaccine they're using.
Modified lives are one that we use pretty commonly.
Killed vaccines are another kind that we use pretty commonly.
Modified lives are interesting because there's a live pathogen in that vaccine, but it's been altered so it won't cause the disease.
But in order to basically activate or bring it back to life, we have to mix those vaccines.
They come in two bottles.
One's kind of a sterile sterile diluent that then we use a reverse vacuum to pull it into a cake powder.
And that's what reactivates the vaccine.
So once you mix that vaccine, in order to get the most value out of that product to make sure that it works, we have to use it within about two hours max.
And you probably want to use that sooner rather than later.
You don't want to push that two-hour mark there that I tell you.
One hour is probably better.
So make sure if you're using modified lives, you mix them as you go throughout the day.
Killed vaccines are ready to roll in the form that they're in.
But those ones we want to be very careful about.
And so same with modified lives, all vaccines.
We want to be very careful about temperature.
We need to store them at a cool temperature, usually between 35 and 45 degrees Fahrenheit.
And we also want to be aware of the fact that sunlight or ultraviolet light can really damage those pathogens that are in there that we're trying to create the immune response with.
So keeping them out of sunlight, keeping them cool, and making sure we mix modified lives as we go is very important.
Right.
And when we're thinking about mixing and using our vaccines, a lot of us, myself included, we have these vaccine guns, these syringes that give multiple dosage.
A lot of them are really great because they're set up to almost be idiot-proof in a kind of a way that, we have a 50 mil and a 25 mil.
In the 50 mil, we can load up our vaccine that requires five cc's, and it gives 10 doses.
And we're done and we're ready to reload.
We get a new needle, and our 25 cc takes care of our 2.5 mil doses in the vaccine.
And same thing, we run out on both those at the same time.
We can change that needle out like we should, and we can go on with our next little group of 10 caps.
Yeah, that's a good point.
So changing needles is really, really important to BQA.
The other thing, when you talk, Scott, about your vaccine guns, I mentioned the UV light there.
Some of those guns that have kind of an amber colored coating on the barrel, so that once you get product in the barrel, it's protected from UV light.
So think about that when you're out there.
You're not just throwing vaccine guns around and letting what's in the barrel be exposed to UV light.
And then also, like you mentioned, changing needles.
BQA guidelines say change needles every 10 to 15 heads.
So a really good reminder, a rule of thumb is exactly like you described.
Once you get done with whatever's in the barrel of that vaccine gun, go ahead and change your needle.
And make sure that you change the needle before you draw up the next round of vaccine, because otherwise a dirty needle in a vaccine bottle contaminates the entire bottle.
So make sure it's fresh and sterile before you draw up that next round.
And go ahead and do it that way.
And so when we're thinking about giving these vaccinations, and maybe we're giving some other things as well, maybe a B12 shot, maybe a multiple mineral injection of some kind, where on the body do we need to remember to always give those injections at?
Yeah, this is the basics BQA principle.
Everybody knows it.
For the most part, I'd like to say we always talk about giving injections in the neck and in the injection triangle.
And so I think sometimes, especially at branding, when we're talking about focusing on our baby calves, and depending on how we've got it set up to do it, it might be challenging to actually get an injection in the neck.
And some folks have said, well, you know, the way we do it, we always give an injection behind the front leg, kind of in the elbow area.
And they've kind of gotten away with that.
And it works okay for them, especially with how maybe they're wrestling calves and they're stretching them out, and they don't have good neck access.
And I just want to make sure to steer everybody away from doing that.
Maybe you've gotten away with it so far and you haven't had any challenges.
But bottom line is that all of our high priced cuts of meat are behind the shoulder.
So stay ahead of the shoulder.
If you give injections in the neck, when those calves go all the way through the process and they end up at slaughter and they become beef, it is so much easier for the packing plant to identify potential abscesses.
If they're all in one location, if they're all in the neck, if all they got to do is look at those necks and trim out from that point, it's so much easier.
But beyond that, something that might be a little bit practical to understand at the ranch is that if you give those injections in that elbow area, there is a lot of nerve endings, nerve bundles, blood vessels in that area.
And we could potentially cause damage to those from an anatomy standpoint, and it could potentially cause paralysis.
So not giving injections there is a really preventative measure.
The other thing is, if you create abscesses in that location, if you give injections there on your calves, it is really challenging to identify and find those and provide care for those abscesses in that area for those calves.
So those are a couple of things to think about.
I know that's kind of a common area, especially for small animals.
I hear people say, well, that's where the veterinarian say I should do this on my lambs or my goats.
On the beef side of things, let's try to make some adjustments if we can to get those injections in the neck, in front of the shoulder, below the nuchal ligament, kind of above the spinal column in that really good triangle.
If you're using a calf table, you probably have good access.
If you're using maybe one of those Nord forks, you'll probably have good neck access.
If you have been trained to stretch those calves for branding and put your knee on the neck, obviously you don't want to put yourself in a compromised position by potentially getting stuck with a needle on the knee or leg.
So there are some ways that you can adjust at that point to maybe move back and straddle the head and make the neck available.
And that's really just the safest way, the safest location, not only for people, but also for the animal, for their welfare, and then for meat quality down the line.
Right.
And a lot of this comes back all the way to the first set of points about preparing the branding crew and knowing what we need to do.
Like, you know, if our brand needs to go on the left side, let's make sure these calves that go in the calf cradle or if we're working them on the ground, that we've got the left side up.
We're not having to give injections on one side and then roll them over to give a brand or vice versa, because that's even more stress on that poor calf that's going through having a bad day to begin with.
But, you know, we need to think about those things.
And when we are giving those injections, we also want to make sure we space them out.
Like I said, it may just be two vaccinations or we may be giving some other additional things.
But, you know, BQA talks about, you know, making sure we have about four inches, which is about the width of your hand across the main knuckles there.
I mean, we don't want to see anybody putting their hand down and trying to put a needle in on one side of their hand and a needle on the other.
But just visually spread them out in that triangle of the neck, at least that four inches or so, so they don't interact with each other and we get the full effectiveness that we want out of those medications.
Yeah, absolutely.
That hand widths rule, it does work really well on bigger calves because you've got a little more space on your canvas, if you will, of where you can give shots.
So just be aware that we need to try to keep about four inches in between.
So being thoughtful about how you space those injections out on those necks, even if they are kind of little at that point, is very, very important so we don't get any reactivity or things like that with what we're giving them.
Right, right.
Well, Libby, we appreciate you coming on the podcast today.
And if people have questions about Beef Quality Assurance, how can they get a hold of you?
Yeah, so we do have a website here in Colorado, it's cobqa.org.
There are a ton of resources on the National BQA's website, including free modules that you can take 24/7 to earn your certification.
The national website is just bqa.org.
Or if you want to talk to me in person, you can always give me a call here.
I'm on campus at Colorado State University and I drew the lucky phone number, I'm 970-491-BEEF.
So 970-491-2333.
Perfect.
Well, again, thank you Libby for being with us on the podcast.
And if you are out there and you have any questions about our discussion today or you have topic ideas that you would like to share, you can always contact me, Scott Stennett, at the Kit Carson County Extension Office at 719-346-5571.
And my colleague who's missing today, Travis Taylor, you can reach him in the Yuma County Extension Office at 970-332-4151.
And again, thanks for listening and joining us here on Pasture to Profit Podcast.
We hope to see you next time.
[Music]