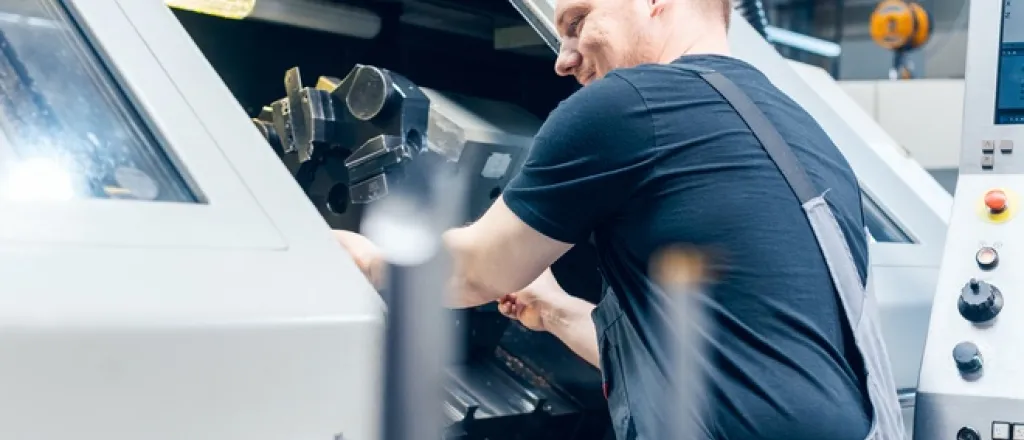
Decisions to make when your tooling budget is small
©
When working with a small tooling budget, strategic decision-making becomes critical to your project’s success. Whether you’re launching a new product or scaling production, every dollar counts.
By focusing on practical, cost-saving measures, you will stretch your budget while maintaining quality and efficiency. Learn four strategies worth considering for better decision-making, making your small budget feel astronomical.
Identify the features that truly matter
The first and most important step is to prioritize essential features. Not every element of your project may be critical for functionality or performance. Start by understanding the core requirements of your product and eliminate unnecessary design complexities. For instance, simplify aesthetic choices that drive up tooling costs without adding significant value.
Focusing on purpose over perfection is especially relevant if you’re in the prototyping phase. A streamlined design reduces the time and resources required for production. Many companies find that this approach saves on expenses and speeds up the timeline to launch.
Leverage cost-effective materials
One way to manage costs without sacrificing performance is by selecting more affordable materials. After all, tooling doesn’t have to always rely on expensive metals or specialized composites.
Advanced aluminum alloys offer durability at a fraction of the cost compared to hardened steel tools. Similarly, plastic molds are an excellent choice for low-volume production or when working on a proof of concept.
Another consideration is knowing when to use reaction injection molding (RIM). Reaction injection molding involves injecting liquid components into a mold, which then chemically reacts to form a solid part. This process is particularly useful for producing large yet lightweight parts or prototypes without the expense associated with traditional injection molding techniques.
Refine your part design
Optimizing your part design minimizes materials and influences tooling expenses considerably. Simple design tweaks, such as reducing undercuts and limiting thin walls, will make your mold easier and cheaper to produce. Collaborate with engineers and designers to identify areas where you can improve functionality with fewer complexities.
For examples of cost-effective designs, look to industries that work with high precision but are cost-sensitive. Aerospace and automotive manufacturers often implement their designs with minimal allowances for additional finishing touches, which reduces tooling cycles and ultimately saves resources.
Outsource wisely
Strategically outsourcing parts or phases of your tooling process will unlock significant savings. Identify regions or suppliers that specialize in low-cost, high-quality manufacturing to keep your overhead manageable. Outsourcing doesn’t always mean a compromise in quality. Many vendors provide rigorous quality control processes built into their service offerings.
However, it’s essential to vet suppliers carefully. Look for partners with industry experience and proven results, especially if they offer transparent pricing. Negotiation will also go a long way when outsourcing multiple aspects of a project. Businesses that bundle production and tooling in one facility may stand to offer better economies of scale.
A small tooling budget requires careful strategies and quick decision-making. Start with these ideas to get the quality you’re looking for without the burden of monetarily exhaustion.